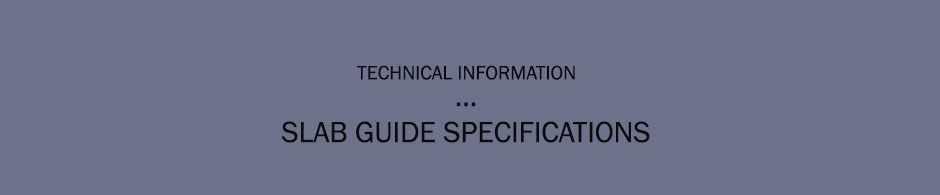
SLAB GUIDE SPECIFICATIONS
PART 1 GENERAL
1.1 SUMMARY
A. Furnish materials, labor, transportation, services, and equipment necessary to furnish and install Quartz Slabs per manufacturer’s recommendations and as indicated on drawings and as specified herein.
B. Provide substrate cabinetry, framing or other to support Quartz surfacing within specified tolerances and according to manufacturer’s specifications.
C. Templates showing cutouts for sinks or cook-tops.
1.2 REFERENCES
A. American Society of Testing Materials (ASTM):
1. ASTM C-170
2. ASTM C-97
3. ASTM C-880
4. ASTM C241
5. ASTM C1028
6. RD2234
B. Performance Requirements
1. Compressive Strength at the time of delivery to be not less than 30,000 psi; averaging 32,000 psi when tested in accordance with ASTM C-170.
2. Water Absorption shall not be greater than 0.02%, when tested in accordance with ASTM C-97.
3. Flexural Strength shall not be less than 7000 psi average when tested in accordance with ASTM C-880.
4. Static Coefficient of Friction ASTM C-1028 conditionally slip resistant:
a. Wet: 0.41 – 0.71 depending on finish
b. Dry: 0.79 – 0.77 depending on finish
1.3 QUALITY ASSURANCE
A. Manufacturer: Company specializing in the manufacture of Quartz engineered stone.
B. Installation shall be by a contractor and crew with at least (1) year of experience in working with Quartz Tile & Slab.
C. Installation Contractor shall conform to all local, state/provincial licensing and bonding requirements.
1.4 SUBMITTALS
A. Submit fabrication and installation instructions as recommended by European surfaces.
B. Submit sample sets of units to indicate color and finish selections. Color & finish will be selected by Architect / Designer / Owner from manufacturer’s available colors. EuroStone Los Angeles, CA. Submit samples of stone joint for color match.
C. Shop drawings showing field verified dimensions, location and dimensions of cutouts, edge profiles and installation details.
D. Submit fabricator’s qualification and certification.
1.5 PROJECT CONDITIONS
A. Do not install during heavy rain or snowfall.
B. Environmental Temperature must be between +5 C and +30 C.
C. The humidity of the foundation must be less than 3%.
1.6 PRODUCT DELIVERY, STORAGE AND HANDLING
Packaging and Shipping: Observe manufacturer’s recommendations to prevent damage. Transport in near vertical position and brace. Transport slabs face to face. Storage: Store in dry, covered area, away from direct exposure to sun.
1.7 WARRANTY
Manufacturer/Installer shall warrant installed system for a period of one year from date of substantial completion against failure of workmanship and materials.
PART 2 – PRODUCTS
2.1 Quartz slabs
A. Manufacturers
1. Acceptable Manufacturer
EuroStone, Los Angeles, CA, (310)967-8000 www.eurostone.us
2.Drawings and installation specifications are based on manufacturer’s proprietary literature from EuroStone. Other manufacturers shall comply with the minimum levels of material specifications and detailing indicated on the drawings or specified herein.
2.2 MATERIALS
A. Crushed Minerals
B. Silica Sand
C. Resin Binder
D. Pigments
E. Various recycled materials
F. Sealer: Colorless, slip and stain resistant penetrating made specifically for Quartz surfacing.
2.3 MANUFACTURED UNITS
A. Slabs
1. Thickness: 13 mm (1/2″ nominal) | 20 mm (3/4″ nominal) | 30 mm (1-1/4″ nominal)
2. Size (56″x120″ nominal), (63″x126″ nominal)
3. Prepolished and calibrated.
4. Finish: Polished or Grain finish (honed).
5. Color: (From Eurostone color chart.)
2.5 Manufacturing process
A. Mechanically vibrated in the molds.
B. Hydraulically pressed under vacuum.
C. Cured in heat chambers.
D. Factory finish: In-line grinding and polishing.
PART 3 – EXECUTION
3.0 FABRICATION
1. Layout to minimize the number of joints.
2. Inspect material for defects or damage prior to fabrication.
3. Inspect material to bear the same batch number. Visually inspect material for adjacent pieces to assure acceptable color match.
4. Cut and polish with water cooled tools only.
5. Cutouts shall have 3/8″ minimum inside corner radius. Polish exposed edges.
6. Laminate layers of material to create built-up edges as required.
3.1 EXAMINATION
A. Inspect substrate areas to receive slab for damage:
1. Verify finished dimensions.
2. Verify that substrate is plumb, level and flat to within 1/16″ in ten feet.
3. Verify that supporting cabinets are securely fix to each other and back wall.
3.2 INSTALLATION
A. Install material per manufacturer’s recommendations
B. Preliminary installation and adjustment. Position material to verify correct fit. Make necessary adjustments. Use water cooled tools.
1. Allow 1/16″ joint between walls.
2. Shim countertop slightly to drain towards sink.
C. Permanent installation.
1. After verifying fit, clean substrate and back of Quartz slab of dust, grease and contaminants.
2. Apply sufficient quantity of mounting adhesive in accordance to manufacturer’s recommendations to provide permanent installation.
D. Joints between Quartz pieces:
1. Shall be tight, flush and level.
2. Securely attached with stone adhesive.
3. Seal joints between the top, backsplash, sink, etc. with silicone sealer.
3.3 CLEANING
A. Remove excessive adhesives and sealant. Clean the surface.
END OF SECTION